¾ó¸¶³ª ¹°µé¾ú³ª¡¤¡¤¡¤¿°»ö »óÅÂ, ½Ç½Ã°£À¸·Î È®ÀÎÇÑ´Ù
2020.03.17
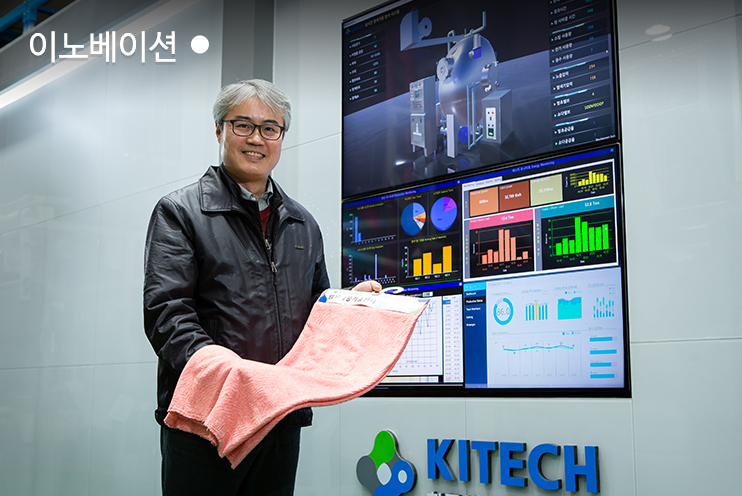
¡ã½ÉÀçÀ± Çѱ¹»ý»ê±â¼ú¿¬±¸¿ø À¶ÇÕ»ý»ê±â¼ú¿¬±¸¼Ò ½º¸¶Æ®¼¶À¯±×·ìÀåÀÌ ¿ø´ÜÀÇ ¿°»ö »óŸ¦ ½Ç½Ã°£À¸·Î ºÐ¼®ÇØ ¿°»ö Á¶°ÇÀ» ÃÖÀûÈÇÒ ¼ö ÀÖ´Â ±â¼úÀ» °³¹ßÇß´Ù. ¨ÏÇѱ¹»ý»ê±â¼ú¿¬±¸¿ø
ÃÖ±Ù À¯ÇàÇÏ´Â Á¦Á¶À¯ÅëÀϰýÇü(SPA) ºê·£µå ¸ÅÀåÀ» °¡º¸¸é ÇѰ¡Áö »ö±òÀÇ ¿ÊÀÌ °É·ÁÀÖ´Â ¸ð½ÀÀ» º¼¼ö ÀÖ´Ù. ½ÇÁ¦ ÀÌ ¿ÊµéÀÇ »öÀº ¸ðµÎ °°À»±î. ÀÌ´Â ¿Ê°¨ ¿ø´Ü¿¡ ´Ù¾çÇÑ »öÀ» ÀÔÈ÷´Â ¿°»ö »ê¾÷°è°¡ °í¹ÎÇÏ´Â ³Á¦À̱⵵ ÇÏ´Ù. ÇÑ ¹øÀÇ ¿°»ö°øÁ¤À¸·Î ¿øÇÏ´Â »öÀ» Á¤È®È÷ ¸¸µé¾î³»¾ß Çϱ⠶§¹®ÀÌ´Ù.
½ÉÀçÀ± Çѱ¹»ý»ê±â¼ú¿¬±¸¿ø À¶ÇÕ»ý»ê±â¼ú¿¬±¸¼Ò ½º¸¶Æ®¼¶À¯±×·ìÀå ¿¬±¸ÆÀÀº ÃÖ±Ù ¿°»ö¿¡ ¾²ÀÌ´Â ¿°¾×À» ºÐ¼®ÇØ »öÀÌ ÀÏÁ¤ÇÏ°Ô À¯ÁöÇϵµ·Ï µ½´Â ¸ðµâ ÀåÄ¡¸¦ °³¹ßÇß´Ù. »ç¶÷ÀÇ Ç÷¾× °Ë»ç·Î °Ç° »óŸ¦ ÆÇ´ÜÇÏµí ¿°»ö±âÀÇ ¿°¾×À» ºÐ¼®ÇÏ¿© ¿°»ö ÁßÀÎ ¿ø´ÜÀÇ »ö»óÀ» ½Ç½Ã°£À¸·Î ¿¹ÃøÇÏ´Â ±â¼úÀÌ´Ù.
ÀϰüµÈ »ö»ó ±¸Çö ¾î·Á¿î ¿°»ö »ê¾÷ ³Á¦
¿°»ö»ê¾÷¿¡ ¾²ÀÌ´Â ¿°»ö ¹æ¹ýÀº °£´ÜÇÏ´Ù. ¿°»ö±â¿¡ ¿ø´ÜÀ» ³Ö°í ¿°·á°¡ µé¾î°£ ¿°¾×À» ä¿î µÚ ¿ÊÀ» »¡µí ¿Ê°¨À» ¹Ýº¹Çؼ ¿°¾× ¼Ó¿¡ ´ã°¬´Ù »©´Â ¹æ¹ýÀÌ´Ù. ƯÁ¤ »öÀ» ³»´Â ¿°·á¸¦ ¹èÇÕÇÑ ¿°¾×À» ä¿ì°í ¿°·á¸¦ ¹è¾îµé°Ô ÇÒ ¿°±â¼º ¿ë¾×À» ÷°¡ÇÏ¸é ³ª¸ÓÁö ºÎºÐÀº ±â°è°¡ ¼öÇàÇÑ´Ù. ¿°»öÀ» ¸¶Ä£ ´ÙÀ½ ´Ù½Ã »¡·¡ÇÏµí ±ú²ýÇÑ ¹°¼Ó¿¡ ¿Ê°¨À» ´ã°¬´Ù »©¸ç À¯ÇؼººÐÀ» Á¦°ÅÇÏ´Â ¡®¼ö¼¼¡¯ ´Ü°è¸¦ ¿©·¯ Â÷·Ê °ÅÄ¡¸é ¿øÇÏ´Â »ö»óÀÇ ¿Ê°¨ÀÌ ¸¸µé¾îÁø´Ù.
ÇÏÁö¸¸ ¿øÇÏ´Â »öÀ» ¿Ê°¨¿¡ ¹è°Ô ÇÏ´Â ÀÏÀº ½±Áö ¾Ê´Ù. ±â°è ¿À·ùºÎÅÍ Àΰ£ÀÇ ½Ç¼ö±îÁö ¿°»ö°úÁ¤¿¡¼ ¹ß»ýÇÏ´Â ¿©·¯ °¡Áö ºÒ·®¿äÀÎ ¶§¹®¿¡ÀÌ ÀÖ´Ù. ÇöÀå¿¡¼´Â À̸¦ ¸·±â À§ÇØ ¼÷·ÃµÈ Àü¹®°¡µéÀÌ ¼öÀÛ¾÷À¸·Î °ü¸®ÇÑ´Ù. ÇÏÁö¸¸ »ç¶÷ÀÌ ÇÏ´Â ÀÏÀ̶ó ¸Å¹ø Á¤È®ÇÑ »ö»óÀ» ±¸ÇöÇϱ⠽±Áö ¾Ê´Ù.
¡ã½ÉÀçÀ± ½º¸¶Æ®¼¶À¯±×·ìÀåÀÌ ¿°»ö Á¶°ÇÀ» ÃÖÀûÈÇÏ´Â ±â¼úÀ» ¼³¸íÇϰí ÀÖ´Ù. ¨ÏÇѱ¹»ý»ê±â¼ú¿¬±¸¿ø
¿°»ö±â¸¦ ´Ý°í ¿°»öÀ» ½ÃÀÛÇϸé Áß°£¿¡ ¸ØÃ߱⠾î·Á¿ö ¿°»öÀÌ ³¡³ µÚ ¿ø´ÜÀ» º¸°í ³ª¼¾ß »öÀÌ Á¦´ë·Î ³ª¿Ô´ÂÁö¸¦ ¾Ë ¼ö ÀÖ´Ù. ½É ±×·ìÀåÀº ¡°1ȸ ¿°»ö ½Ã ÇÏ´Â µ¥ 2~3½Ã°£ÀÌ °É¸®´Âµ¥ »öÀÌ ¸ÂÁö ¾ÊÀ¸¸é ´Ù½Ã ¿ø´ÜÀ» ³Ö°í »öÀ» ¼öÁ¤ÇÑ ÈÄ ¿°·á¸¦ ´Ù½Ã Áý¾î³Ö´Â °úÁ¤À» °ÅÄ£´Ù¡±¸ç ¡°½Ã°£µµ 2¹è °É¸±»Ó´õ·¯ ¿°»ö¿¡ ¾²´Â ¿°·á¿Í ¹°, ¿¡³ÊÁö, Æó¼öµµ 2¹è ¹èÃâµÇ´Â ¹®Á¦°¡ ÀÖ´Ù¡±°í ¸»Çß´Ù.
¿°¾× ½Ç½Ã°£ ºÐ¼® ±â¼ú °³¹ßÇØ ¹° »ç¿ë·®µµ Àý°¨
¿¬±¸ÆÀÀº ¿ø´ÜÀ» º¸´Â ´ë½Å ¿°¾×¿¡ ÁÖ¸ñÇØ ±× »óŸ¦ ½Ç½Ã°£ °üÂûÇÒ ¹æ¹ýÀ» ã¾Ò´Ù. ¿°»öÀº ¿°¾× ¿ø·á¸¦ ¿ø´Ü¿¡ ºÙÀÌ´Â ¿ø¸®´Ù. ¿°»öÀ» ½ÃÀÛÇÏ¸é ¿ø´Ü¿¡ ¼¼È÷ ´Þ¶óºÙ´Âµ¥, ÀÌ °úÁ¤¿¡¼ ¿°¾× ¼Ó ¿°·áÀÇ ³óµµ°¡ ¿¶¾îÁø´Ù. ¿°¾×À» ºÐ¼®ÇÏ¸é °Å²Ù·Î ¿ø´Ü¿¡ ¾ó¸¶³ª ¿°·á°¡ ´Þ¶óºÙ¾ú´ÂÁö¸¦ ¾Ë ¼ö ÀÖ´Ù.
¿¬±¸ÆÀÀº ¿°»ö±â¿¡¼ ¿°¾× ÀϺθ¦ Èê·¯³ª¿À°Ô ÇÑ ´ÙÀ½ À̸¦ ºÐ¼®ÇÏ´Â ±â¼úÀ» °³¹ßÇß´Ù. ¿°¾×ÀÌ Èê·¯³ª¿Ô´Ù°¡ ´Ù½Ã µé¾î°¡µµ·Ï ¸¸µç °ü¿¡ Àڿܼ±(UV) ¼¾¼¿Í »êµµ(pH) ¼¾¼¸¦ ´Þ¾Ò´Ù. UV ¼¾¼´Â ÀÌ¹Ì ¿Ï¼ºµÈ ¿ø´ÜÀÇ »öÀ» ºÐ¼®ÇÏ´Â µ¥ ÁÖ·Î ¾²¿©¿Ô´Ù. ¿¬±¸ÆÀÀº °°Àº ¿ø¸®·Î ¿°¾× ³óµµ¸¦ ÃøÁ¤ÇÏ´Â ¿ëµµ·Î »õ·Ó°Ô °³¹ßÇß´Ù. ¿ø·á°¡ ¾ó¸¶³ª ´Þ¶óºÙÀ»Áö¸¦ °áÁ¤ÇÏ´Â »êµµµµ ÇÔ²² °üÂûÇÑ´Ù. ¿©±â¼ ¿°¾× ³óµµ°¡ ½Ã°£¿¡ µû¶ó º¯ÇÏ´Â °î¼±À» º¼ ¼ö ÀÖ°í, ÀÌ °î¼±ÀÌ ±âÁذú ÀÏÄ¡Çϸé Á¤È®È÷ °°Àº »öÀÌ ³ª¿À°Ô µÈ´Ù.
¡ã½É ±×·ìÀåÀÌ ¿°»ö±â¿¡ ºÎÂøÇÑ ÀåºñÀÇ µ¥ÀÌÅ͸¦ Åä´ë·Î ¿°»ö Á¤µµ¸¦ ºÐ¼®Çϰí ÀÖ´Ù. ¨ÏÇѱ¹»ý»ê±â¼ú¿¬±¸¿ø
ÀÌ ±â¼úÀº ¿°»ö»Ó ¾Æ´Ï¶ó ¼ö¼¼ ´Ü°è¿¡¼µµ Ȱ¿ëµÈ´Ù. ¼ö¼¼ÀÇ ¸¶¹«¸® ¿©ºÎ´Â ¿ø´ÜÀ» »¡¾Æ ³ª¿Â Æó¼ö¿¡ ¿°·á°¡ ÀÖ´ÂÁö¸¦ È®ÀÎÇÏ¸é ¾Ë ¼ö ÀÖ´Ù. »ç¶÷ ÇǺο¡ ¹®Á¦°¡ ¾øÀ¸·Á¸é ¿ø´Ü¿¡¼ ¿ø·á¿Í ¿°±â¼º ¼ººÐÀÌ ¸ðµÎ ºüÁ®¾ß ÇÑ´Ù. ÇÏÁö¸¸ ´«À¸·Î ÀÏÀÏÀÌ È®ÀÎÇÏ±â ¾î·Æ´Ù º¸´Ï ÇöÀå¿¡¼± '¹«Á¶°Ç ¼ö¼¼¸¦ 10¹ø ÇÑ´Ù'´Â ½ÄÀ¸·Î Á¶°ÇÀ» ³Ö´Â´Ù. ÀÌ ±â¼úÀ» Ȱ¿ëÇÏ¸é ¿ø´Ü¿¡¼ À¯Çع°ÁúÀÌ ³ª¿ÀÁö ¾Ê´Â ½ÃÁ¡À» Á¤È®È÷ ¾Ë ¼ö ÀÖ´Ù. ±×¸¸Å ³¶ºñµÇ´Â ¹°ÀÌ ÁÙ¾îµç´Ù.
½ÇÁ¦·Î ÀÌ ±â¼úÀ» Ȱ¿ëÇϸé ÇÑ ¹ø¿¡ °°Àº »öÀÌ ³ª¿Ã È®·üµµ Å©°Ô ¿Ã¶ó°£ °ÍÀ¸·Î È®ÀεƴÙ. ¿°»ö °øÁ¤¿¡¼ °°Àº »öÀÌ ³ª¿À´Â ºñÀ²ÀÎ ¿°»ö ÀçÇö¼ºÀº 95%·Î ³ªÅ¸³µ´Ù. ¿°»ö½Ã°£Àº 25%, ¼ö¼¼ ½Ã°£µµ 30% ÁÙ¾ú´Ù. ½É ±×·ìÀåÀº ¡°¿°»ö¿¡¼ ¾²ÀÌ´Â ¹°ÀÌ 1tÀ̶ó°í ÇÏ¸é ¼ö¼¼¿¡ ¾²ÀÌ´Â ¹°Àº 10t¿¡ À̸¥´Ù¡±¸ç ¡°¼ö¼¼¿¡¼ ¾²ÀÌ´Â ¹°À» ¾Æ³¢¸é¼ 20% Á¤µµÀÇ ¹° Àý°¨ È¿°ú¸¦ ¾ò¾ú´Ù¡±°í ¸»Çß´Ù. ¹°À» ¾Æ³¥»Ó ¾Æ´Ï¶ó Æó¼ö°¡ ¹æÃâµÇ´Â °ÍÀ» ¸·±â ¶§¹®¿¡ 'Àϼ®ÀÌÁ¶' È¿°úµµ °Åµ×´Ù.
Á¤È®ÇÑ »ö ±¸ÇöÇÏ´Â ¿ÏÀüÀÚµ¿È ±â¼ú °³¹ßÇÒ °Í
ÀÌ ±â¼úÀº »ý±â¿ø ³»ºÎ°úÁ¦¸¦ ¹Þ¾Æ 3³â¿¡ °ÉÃÄ °³¹ßµÆ´Ù. ƯÇã Ãâ¿ø 7°Ç°ú µî·Ï 5°Ç, ±â¼úÀÌÀü 4°ÇÀÇ ¼º°ú¸¦ ³Â´Ù. ¶Ç Áö³ÇØ »ê¾÷Åë»óÀÚ¿øºÎ°¡ 60¾ï ¿ø ±Ô¸ð·Î ¸¶·ÃÇÑ Áö´ÉÇü ¿°»ö°øÀå »ç¾÷À» À̲ø¾î³½ °è±â°¡ µÇ±âµµ Çß´Ù. ¿¬±¸ÆÀÀº ¿°»ö Àü¹®±â¾÷°ú Çù¾àÀ» ¸Î°í ½º¸¶Æ®°øÀåÀ» ±¸ÃàÇÏ´Â »ç¾÷À» ÁøÇàÇÒ °èȹÀÌ´Ù.
¡ã½É ±×·ìÀå°ú ¿¬±¸¿øµéÀº ¿°»ö ÀÚµ¿È ¼³ºñ¸¦ ³Ñ¾î Áö´ÉÇü ¿°»ö°øÀåÀ» ±¸ÃàÇÏ´Â »ç¾÷À» °èȹÇϰí ÀÖ´Ù. ¨ÏÇѱ¹»ý»ê±â¼ú¿¬±¸¿ø
¿¬±¸ÆÀÀº ¸ðµâÀÌ Á¦°øÇÏ´Â Á¤º¸¸¦ Åä´ë·Î ¿°»ö±â¿¡¼ Á¤È®ÇÑ »öÀ» ±¸ÇöÇÏ´Â ¿ÏÀüÀÚµ¿È ±â¼úÀ» °³¹ßÇÏ¸é ¿°»ö°øÀåÀ» ½º¸¶Æ®È ÇÒ ¼ö ÀÖÀ» °ÍÀ¸·Î ±â´ëÇϰí ÀÖ´Ù. Áö±ÝÀº ¿°»ö±â¿¡ ¿°·á³ª ÈÇÐ ¾àǰÀ» Áý¾î³Ö´Â ÀÛ¾÷À» ¸ðµÎ ¼öÀÛ¾÷À¸·Î Çϰí ÀÖÁö¸¸, ½É ±×·ìÀåÀº ¡°¿°»ö±â¿¡ ¾Æ¹«·± ½Å°æ ¾µ ÇÊ¿ä ¾øÀÌ ¹°°ú ¿ø´Ü¸¸ ³ÖÀ¸¸é ¾Ë¾Æ¼ ¿°»öÀ» ¸¶¹«¸®ÇÏ´Â ±â¼úÀ» °³¹ßÇÒ °èȹ¡±À̶ó°í ¸»Çß´Ù. ¿°»ö±â¿¡ ¿°·á¿Í ¿ë¾×À» ÀúÀåÇÏ´Â ÀåÄ¡¸¦ ´Þ¾Æ ¿øÇÏ´Â ¿°»ö »ö»ó¿¡ ¸Â°Ô ÀÚµ¿À¸·Î ÁÖÀÔ ÇÒ ¼ö ÀÖÀ» Àü¸ÁÀÌ´Ù.
¿ÏÀüÀÚµ¿È°¡ ÀÌ·ïÁö¸é ¡®¸®ÇÇÆ® ¿À´õ¡¯¿¡¼ »ý±â´Â ¹®Á¦µµ ÇØ°áµÈ´Ù. ¸®ÇÇÆ® ¿À´õ´Â ¿°»ö±â°¡ ÇÑ ¹ø¿¡ ó¸®ÇÏÁö ¸øÇÏ´Â ¹°·®À» ¿°»öÇϱâ À§ÇØ °°Àº »öÀ» ¹Ýº¹ÇØ ³»´Â ÀÛ¾÷À» ¶æÇÑ´Ù. Á¦Á¶À¯ÅëÀϰýÇü(SPA) ºê·£µå°¡ À¯ÇàÇÏ¸é¼ ¸®ÇÇÆ® ¿À´õ¸¦ ¼öÇàÇÏ´Â Àϵµ ´Ã¾ú´Âµ¥, ÀÌ ±â¼úÀ» Ȱ¿ëÇÏ¸é °°Àº »öÀ» ±×´ë·Î ±¸ÇöÇÒ ¼ö ÀÖ´Ù. ½É ±×·ìÀåÀº ¡°¿°»ö °î¼±¸¸ ÄÄÇ»ÅÍ¿¡ ³ÖÀ¸¸é Ç×»ó ù ¹øÂ° ¿°»ö °á°ú¿Í °°Àº ¿°»ö¹°À» ¸¸µé¾î³¾ ¼ö ÀÖ´Ù¡±°í ¸»Çß´Ù.
¿¬±¸ÆÀÀº ½º¸¶Æ® ¼¶À¯°øÀå ¸ðµ¨À» ¸¸µé¾î °ª½Ñ ³ëµ¿·ÂÀ» ¾Õ¼¼¿î Áß±¹°úÀÇ °æÀï°ú °¢Á¾ ȯ°æ±ÔÁ¦ ÀÌÁß°í¿¡ Á÷¸éÇÑ ±¹³» ¼¶À¯¾÷°èÀÇ °æÀï·ÂÀ» ³ôÀÌ´Â °Ô ¸ñÇ¥´Ù. ³ëµ¿Áý¾àÀûÀÎ ¿°»ö»ê¾÷¿¡¼ °øÀå ÀÚµ¿ÈÀÇ Çʿ伺ÀÌ Á¦±âµÈ Áö´Â ¿À·¡µÆÁö¸¸ Á¦´ë·Î ±¸ÇöµÇÁö ¸øÇß´Ù. ±×·¯´ø °ÍÀÌ 4³â ÀüºÎÅÍ À̸¦ Çö½ÇÈÇÒ ¼¾¼ ±â¼úµéÀÌ µîÀåÇÏ¸é¼ ¿ÏÀüÀÚµ¿È ±â¼ú¿¡ µµÀüÇØº¼ ¸¸ÇÑ ¿©°ÇÀÌ ¸¶·ÃµÇ°í ÀÖ´Ù. ½É ±×·ìÀåÀº ¡°¾ÆÀ̵ð¾î¸¦ °®°í µµÀüÇÏ´Â ±â¼úÀ» ¸ÕÀú °³¹ßÇØ ³õÀ¸¸é ±Û·Î¹ú Á¦Á¶Çõ½Å ¿ä±¸¿¡ Á÷¸éÇØ ÀÖ´Â ¼¶À¯ ºÐ¾ßÀÇ Áß¼Ò±â¾÷ Áö¿ø¿¡µµ º¸´Ù Àû±ØÀûÀ¸·Î ´ëÀÀ ÇÒ ¼ö ÀÖÀ» °Í¡±À̶ó°í ¸»Çß´Ù.